About Us
About Safar
What we do?
We recycle discarded PET bottles into user friendly polyester staple fibre and polyester spun yarn having versatile applications. To source raw material (Pet plastic waste) we have developed a pan india network of scrap dealers and contractors who in turn work through rag pickers for supplying the PET plastic waste to the Company. Contractors also supply directly from various cities.
PET plastic waste are being crushed and baled at collection centres and recieved in our manufacturing facilities sent to factories for further processing. Network enables collection of about 350 tons of PET plastic waste daily.
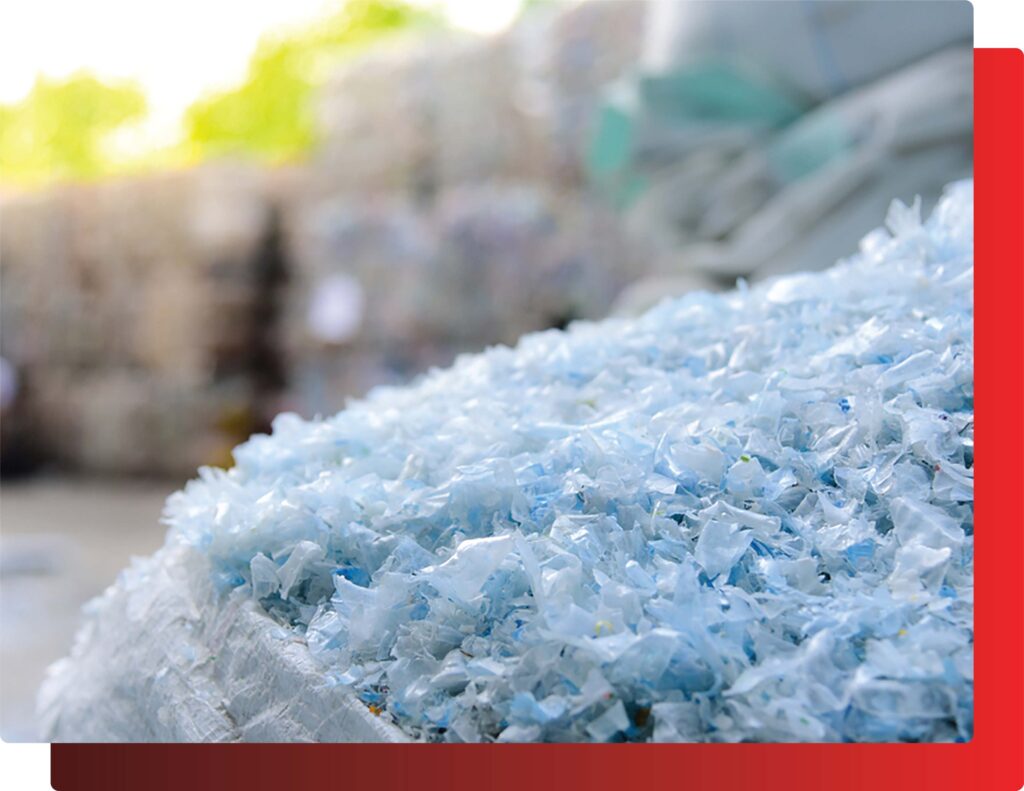
Factory & Process
GALLERY
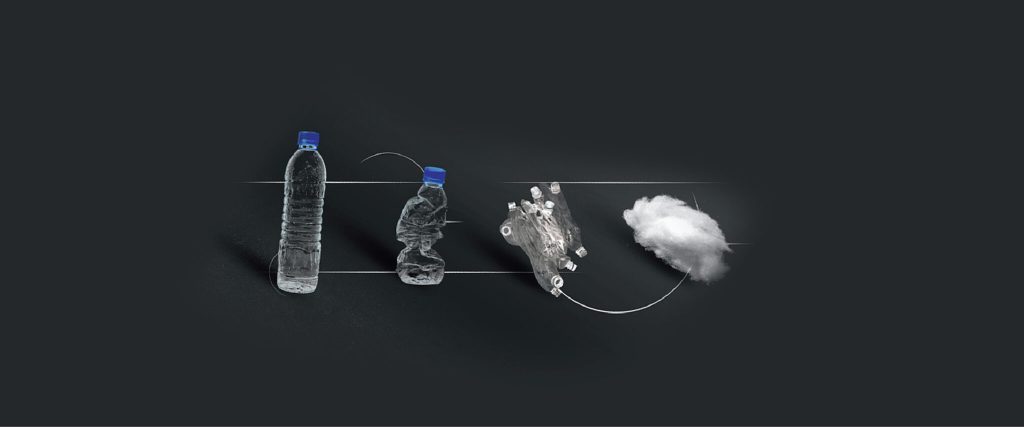
PET bottles are first manually cleaned to remove dirt and foreign objects. Road waste is sorted, cleaned, washed and cut through a specially designed PET treatment wash plant. After this, long-sized waste is fed to the cutters for cutting into smaller sizes for easy handling of the materials. Irregular lumps and blocks of materials are crushed. If the raw waste is of low density, it is compacted through a densifier to get a higher density. The washed, shredded PET bottles are fed into a vacuum dryer to be rid of the moisture. The master batch of pigments is also added in the dryer to produce coloured output materials or for optical brightness, depending on the end use of the product. After this, the dryer unloads the polymer into the hopers connected to the extruder. The extruded polymer in melted form then flows to the spin assembly through filters. Filamentation takes place in the spin assembly through spinnerets having tiny holes all along its circumference.
After spinning, filaments are cooled by air and collected in cans through winders. A steam-heated hot water trough heats the tow to its glass transition temperature for easy drawing. Spin finish is applied to the tow by passing the same through a trough containing finish solution. Siliconised or ordinary spin finish is used, depending on the end use of the fibre. After finish application, the tow is crimped to give curliness to the fibre. Crimps in the tow are heat-set in a kiln, which has multiple heating zones. The tow is heated by air to a particular level, depending on the end use. The heat treated tows are then moved through cutting machines to cut the fibre to the desired length. The loose, staple fibres are then taken to a hydraulic bailing press, where the fibre is pressed and packed in bales, and stored and dispatched.
ABOUT SAFAR
Mission
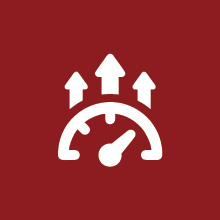
To be a high-performance organization by making the best use of resources and empowering people.
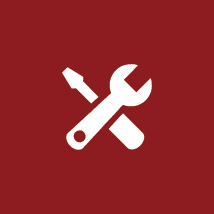
To be the preferred choice of our customers by providing world class customer services.
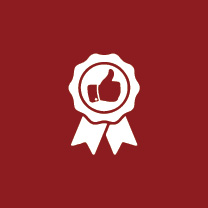
To maintain high levels of quality in our products through innovative research and technology development in our processes,
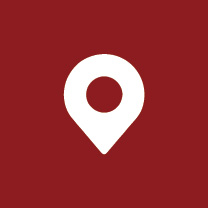
To contribute to the cause of making our planet a better place to live in forthe present and future generations.
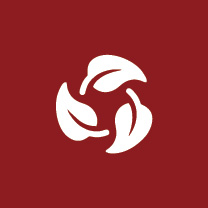
To Change the concept of post consumer pet bottle from waste to eco friendly raw material forthe benefit of all
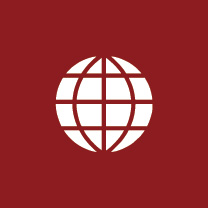
To be a Global Corporate citizen turning our pet waste into valuable products and to do our part in reducing the pollution plaguing our planet
BE PART OF THE SOLUTION
VISION
To make earth better and sustainable place to live in.
To become a Global Corporate citizen committed to recycle
every PET bottle which is thrown into waste with world class recycling facilities.
Our strong & dynamic
Mission
- DELIVERING INNOVATIVE PRODUCTS
- EXCELLENCE IN WHATEVER WE DO
- UNCOMPROMISING INTEGRITY
- RESULTS THROUGH TEAMWORK
- TRUST AND RESPECT FOR EVERYONE
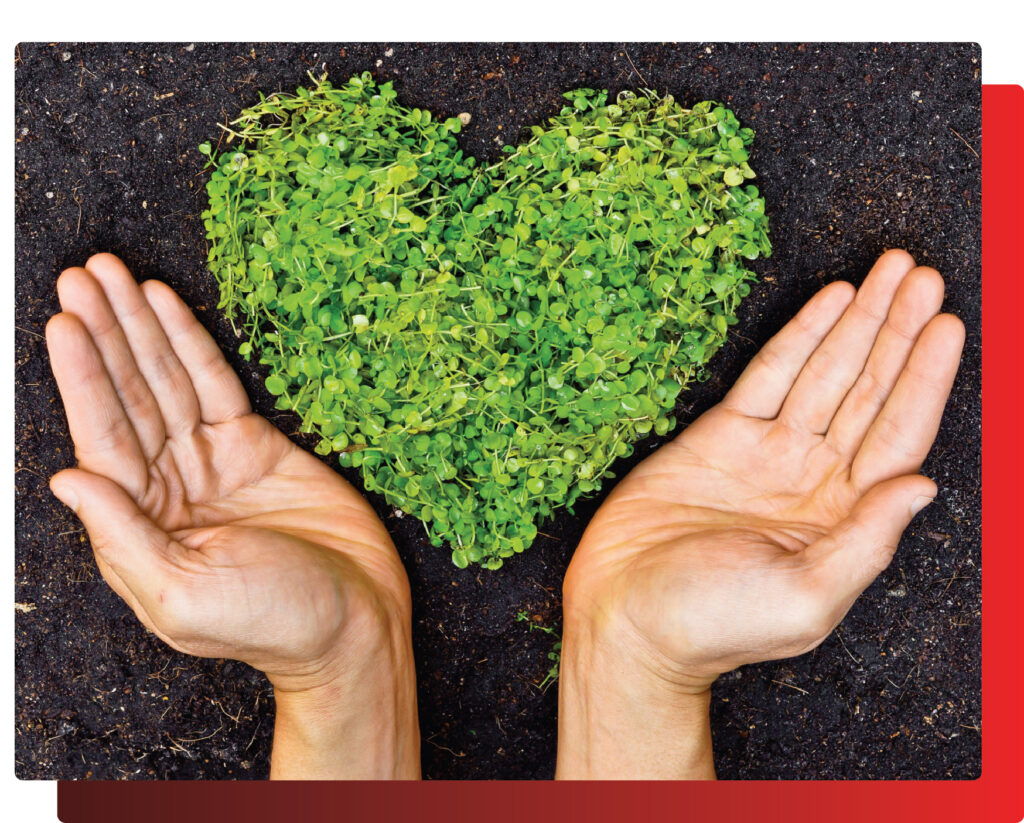